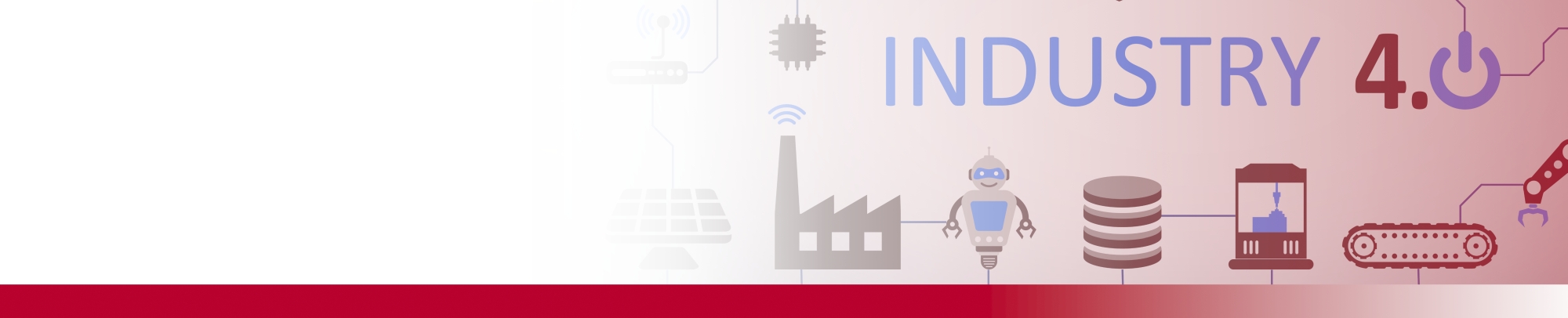
IPAR 4.0
Munkánk során az egyik legfontosabb szempontunknak az Ipar 4.0 által megfogalmazott követelményeknek való megfelelőséget tartjuk, így a fejlesztéshez használt eszközeinket is eszerint választjuk meg.
Az Európai Parlament 2016-ban megfogalmazott állásfoglalása szerint:
Az ipar 4.0 a termelési folyamatok olyan szervezését írja le, melynek keretében az eszközök önállóan kommunikálnak egymással az értéklánc mentén: a jövő egy olyan „okos” gyárát hozva létre ezzel, amelyben a számítógép-vezérelt rendszerek nyomon követik a fizikai folyamatokat, létrehozzák a fizikai valóság virtuális mását és decentralizált döntéseket hoznak önszervező mechanizmusok alapján.
(forrás: Industry 4.0 Policy Department Economic and Scientific Policy, 2016, p 22-23.)
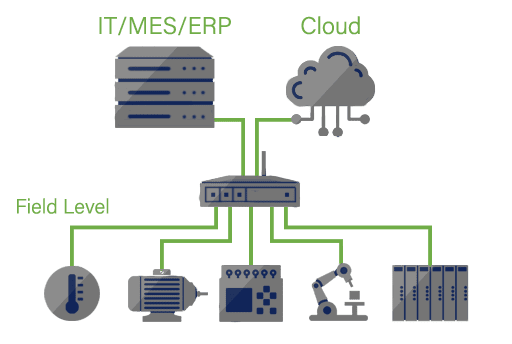
Az IPAR 4.0 megvalósítására a DCS (Distributed Control System) a kézenfekvő megoldás.
A DCS folyamatirányító rendszer integrált, funkcionálisan és területileg elosztott ipari folyamatok hatékony vezérlésére szolgál. Nagysebességű kommunikációs hálózaton együttműködő számítógépeket , intelligens berendezéseket, Real Time (valós idejű) vezérlő eszközöket (PLC) tartalmaznak, amelyek kombinációja az ipari folyamatirányítás széles skáláján alkalmazható egységes rendszert alkot az egyedi gépvezérlésektől a teljes gyárautomatizálási feladatokig.
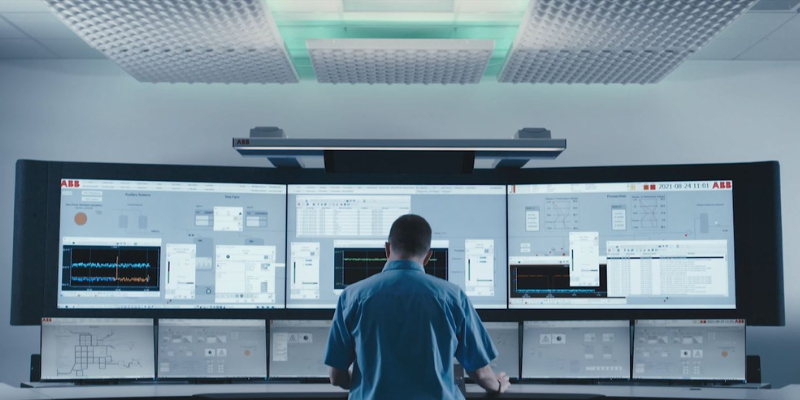
Az első DCS megoldásokat a 80-as évek elején mutatták be. A fejlesztők szándéka egy olyan elosztott intelligenciájú, nagy teljesítményű rendszer megalkotása volt, amely iparágtól függetlenül bármilyen technológiai követelményeknek megfelel, illeszthető bármely méretű és biztonságú feladathoz.
Megjelenésük óta a DCS rendszerek töretlenül fejlődnek, figyelembe véve az IT és kommunikációs technológiák újabb és újabb kihívásait.

DCS evolúció a termelési folyamatok teljes lefedésére (Extended Automation System)
A modern gyárirányítási rendszerek , döntést segítő információs és erőforrás –optimalizáló eszközök ( Manufacturing Execution Sytem (MES), Enterprice Resource Planning (ERP) stb.) egyre több termelési információt igényeltek a DCS folyamatirányító rendszerekből. Igényként jelent meg a DCS rendszerek illesztése más feladatokat ellátó számítógépekhez, valamint a DCS adatainak integrálása a gyárszintű információs adatbázisokba a meglévő üzemi információs hálózaton keresztül.
Ugyancsak követelményként jelent meg a gyári hálózatokon keletkező minőségi és mennyiségi adatok, valamint a termelésre vonatkozó paraméterek visszajuttatása a DCS rendszerbe. Ezen igények kielégítésére a tradicionális Distributed Control System (DCS) átformálódott először (Open Control System ( OCS) -é, majd a további technológiák felhasználásával kialakult az Extended Automation System rendszer elrendezés.
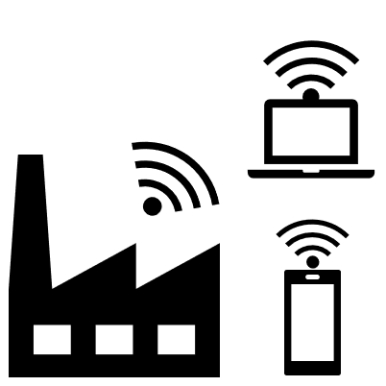
Már nem a minimális egységköltségű tömegtermelés a cél, hanem a költséghatékonyság és a sebesség mellett a személyre szabhatóság is. Jelenleg a technológia rohamos fejlődése sokszor nem ad időt megérteni az újdonságokat.
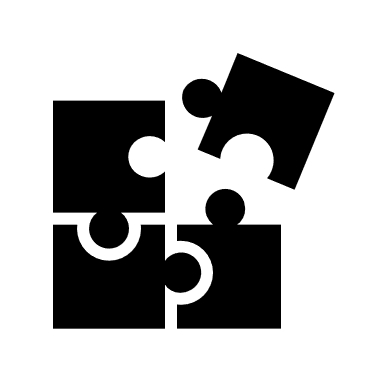
Contro-Net Kft.-nél a folyamatirányítás mellett figyelembe vesszük a szakmai fejlődés és haladás fontosságát. Batch programozással lehetőség van folyamatautomatizálásra emberi beavatkozás nélkül. A MES (Manufacturing Execution System) szabványosított interfészek révén integrálja az összes kapcsolódó IT rendszert, például ERP, LIMS vagy DCS rendszereket, biztosítva ezzel a zökkenőmentes információcserét és a jobb teljesítményt.
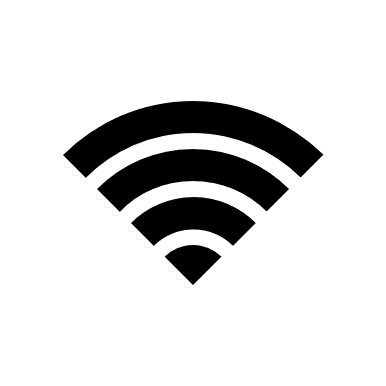
A gyógyszeriparban vagy más technológiákban előállított papír alapú gyártási folyamatok lassúak, hibára hajlamosak és költségesek. Az egyes tételek eltéréseinek jelentős részét emberi hiba okozza. A MES segít kiküszöbölni az emberi mulasztás okozta hibalehetőségeket. Végig vezeti az üzemeltetőket a gyártási folyamaton, és minden lépést irányít. Nincs Ipar 4.0 MES nélkül – vallják a szakemberek. Az IoT olyan gépek közötti hálózatot ad, pl szenzorok, digitális eszközök, szoftverek között, melyek emberi beavatkozás nélkül képesek monitorozni és menedzselni folyamatokat.
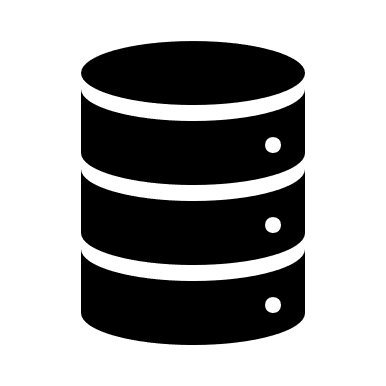
Ipari rendszerek automatizálásához elengedhetetlen a szakszerű adatgyűjtés és riportkészítés. A mai világban fontos szerepet kap az adatgyűjtés és tárolás, valamint ezen, az egyén által kezelhetetlen méretű adathalmazok (Big Data) kiértékelése. Ebbe a feladatban segít a rendszer különböző riportálása. A riportkészítő automatizmus összegyűjti és archiválja a real-time információkat, valamint hozzáfér az archivált adatokhoz is.
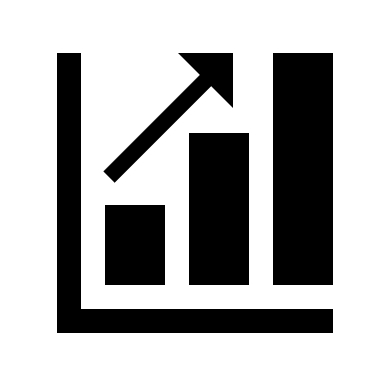
A fejlődésnek nagy előnye, hogy az értéklánc teljességében optimalizálódnak a termelési folyamatok. Az egyedülálló, elavultnak számító gépek is teljesen integrálhatóak és automatizálhatók, melynek következtében növekedhet a termelékenység sebessége, minősége és rugalmassága is. Az öntanuló és paraméterezhető rendszer hozzájárul a hatékonyság növekedéséhez.
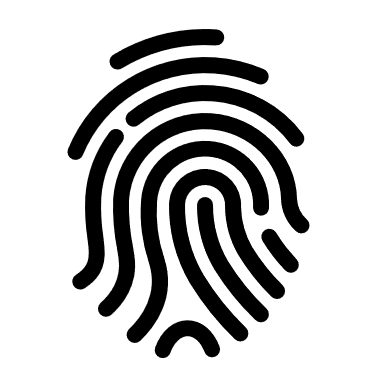
A biztonság valamennyi területen kiemelkedően fontos jelentőséggel bír. Egyik oldalról a rendszer “safety” megbízhatósága, avagy üzembiztossága, ami a működésének folyamatos biztosítása a felhasználók felé. Valamint az adatok security biztonsága, hogy külső illetéktelen fél ne férhessen a rendszer részeihez. A megfelelő jogosultságokkal rendelkező kliensek – legyen ez eszköz vagy személy – léphet kapcsolatba egymással a biztonságos kommunikációt megtartva.
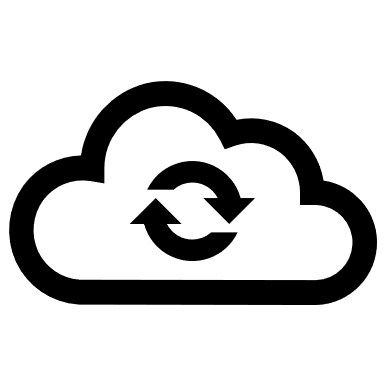
A Smart Factory egy olyan gyártási környezetet foglal magába, ahol a berendezések munkáját önmaguk vagy rájuk telepített központi rendszer vezérli, emberi beavatkozás nélkül. Ennek a technológiai alapját a kiber-fizikai rendszerek alkotják, aminek elemei az IoT segítségével kommunikálnak egymással. Az eljárást nagymértékben optimalizálja, jobb rálátást biztosít a folyamatok részleteire és könnyebb kihozni a maximumot.
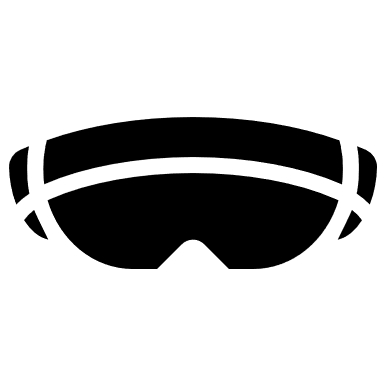
A gyártással egy virtuális rendszert kapcsol össze a digitális gyár. A gyártásról kapott adatok és információk megjelenítésére az AR modern lehetőséget nyújt. Egy szemüvegen keresztül el lehet érni az egyes részegységekhez tartozó adatokat, működési paramétereket többdimenziós átlátható és élethű formában. Valamint ez lehetőséget ad távoli konzultációra, szervízelési és karbantartási segítségekre. Fizikai emberi jelenlét nélkül elvégezhető az ellenőrzés és a vezérlés veszélyes vagy tiszta terekben.

Oldalunk jelenleg fejlesztés alatt áll.
További információkért kérjük lépjen kapcsolatba velünk!