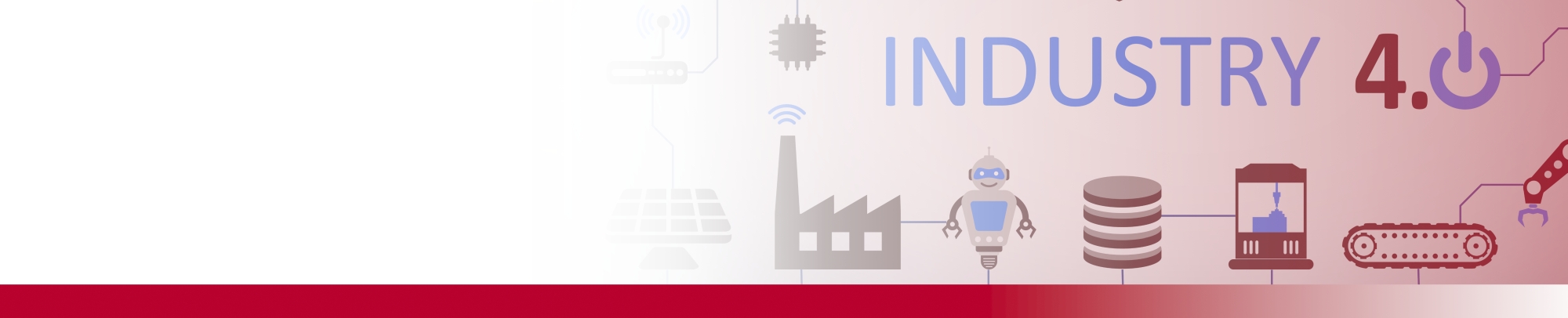
INDUSTRY 4.0
One of our main priorities in our work is compliance with the requirements set by Industry 4.0, which is why we choose our development tools accordingly.
According to the European Parliament's resolution in 2016:
The industry 4.0 describes the organization of production processes in which devices communicate independently with each other along the value chain: this creates the "smart" factory of the future, where computer-controlled systems track physical processes, create a virtual replica of the physical world, and make decentralized decisions based on self-organizing mechanisms.
(source: Industry 4.0 Policy Department Economic and Scientific Policy, 2016, p 22-23.)
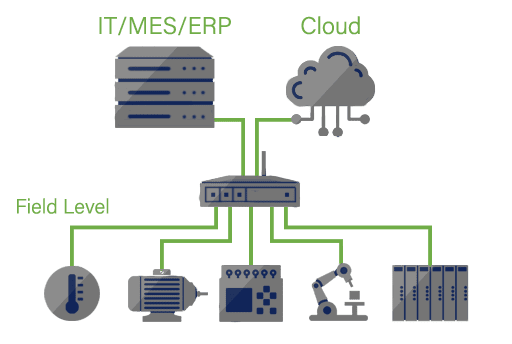
The DCS (Distributed Control System) is the obvious solution for the implementation of Industry 4.0..
The DCS process control system is designed for the efficient control of integrated, functionally and geographically distributed industrial processes. It includes computers, intelligent devices, and Real-Time (PLC) controllers that cooperate over a high-speed communication network. This combination creates a unified system that can be applied across a wide range of industrial process control, from individual machine controls to complete factory automation tasks.
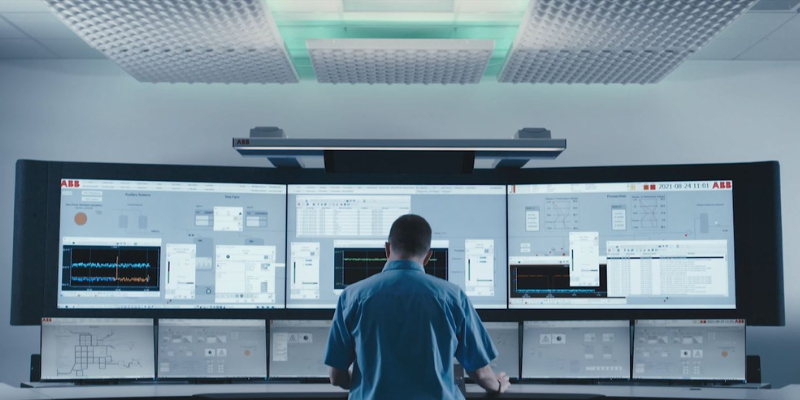
The first DCS solutions were introduced in the early 1980s. The developers' intention was to create a distributed, intelligent, high-performance system that could meet any technological requirements, regardless of the industry, and be adaptable to tasks of any size and safety level.
Since their introduction, DCS systems have continuously evolved, taking into account the ever-growing challenges of IT and communication technologies.

DCS evolution for full coverage of production processes (Extended Automation System).
Modern factory management systems, decision-supporting information tools, and resource-optimizing tools (such as Manufacturing Execution Systems (MES), Enterprise Resource Planning (ERP), etc.) increasingly require production information from DCS process control systems. The need emerged for integrating DCS systems with other computers performing different tasks, as well as integrating DCS data into factory-level information databases through the existing industrial information network.
It also became a requirement to return quality and quantity data generated on factory networks, as well as production-related parameters, back to the DCS system. To meet these needs, the traditional Distributed Control System (DCS) first evolved into an Open Control System (OCS), and then, with the use of further technologies, the Extended Automation System configuration was developed.
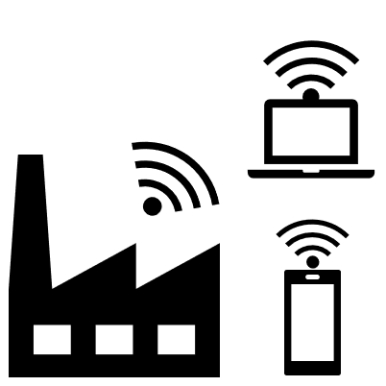
The goal is no longer mass production with minimal unit costs, but rather cost-effectiveness, speed, and customization. Currently, the rapid development of technology often doesn't allow enough time to fully understand the new innovations.
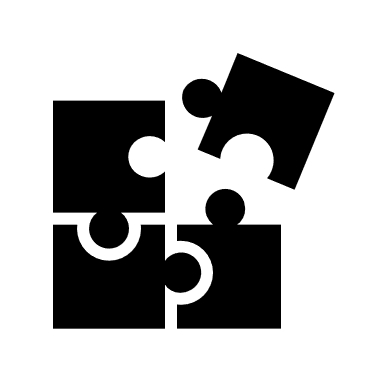
At Contro-Net Kft., alongside process control, we emphasize the importance of professional development and progress. With batch programming, it is possible to automate processes without human intervention. The MES (Manufacturing Execution System), through standardized interfaces, integrates all related IT systems, such as ERP, LIMS, or DCS systems, ensuring seamless information exchange and better performance.
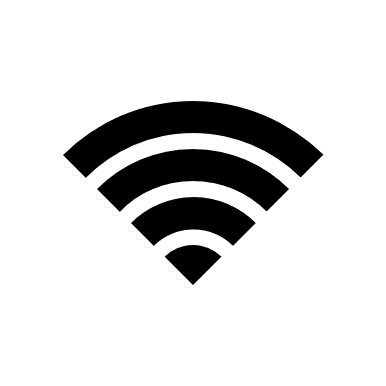
In the pharmaceutical industry or other technologies, paper-based manufacturing processes are slow, error-prone, and costly. A significant portion of the deviations in individual batches is caused by human error. MES helps eliminate the potential errors caused by human omissions. It guides operators through the manufacturing process, directing each step. There is no Industry 4.0 without MES – this is what experts say. The IoT provides a network between machines, such as sensors, digital devices, and software, which can monitor and manage processes without human intervention.
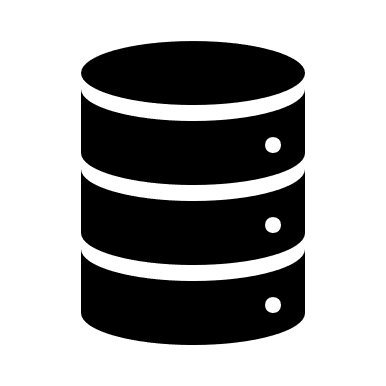
Professional data collection and reporting are essential for the automation of industrial systems. In today's world, data collection and storage, as well as the evaluation of these data sets (Big Data) that are too large for individuals to manage, play a crucial role. The system's various reporting functions assist in this task. The report-generating automation collects and archives real-time information and also has access to archived data.
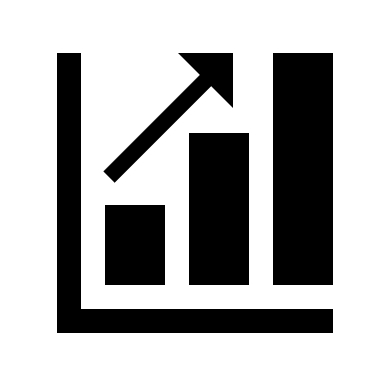
The advantage of development is that production processes are optimized across the entire value chain. Even outdated, unique machines can be fully integrated and automated, resulting in increased productivity in terms of speed, quality, and flexibility. The self-learning and configurable system contributes to the improvement of efficiency.
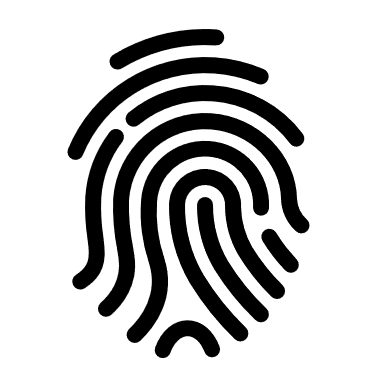
Safety is critically important in all areas. On one hand, there is the system's "safety" reliability, or operational dependability, which ensures the continuous operation for users. On the other hand, there is the data security, preventing unauthorized external parties from accessing the system's components. Only clients with the appropriate permissions—whether devices or individuals—can communicate with each other while maintaining secure communication.
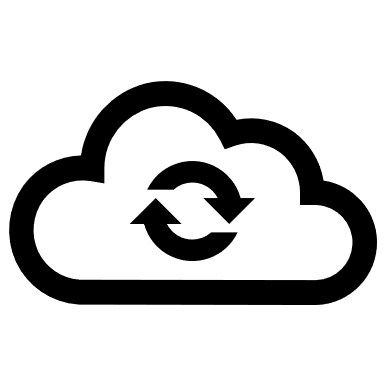
The Smart Factory is a manufacturing environment where equipment is controlled autonomously or by a central system installed on them, without human intervention. The technological foundation of this system consists of cyber-physical systems, whose elements communicate with each other through IoT. This approach significantly optimizes the process, provides better insight into the details of operations, and makes it easier to extract the maximum performance.
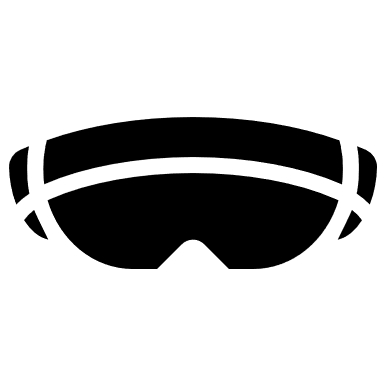
The digital factory connects manufacturing with a virtual system. Augmented Reality (AR) offers a modern solution for displaying data and information gathered from the production process. Through AR glasses, operators can access real-time data and operational parameters of individual components in a clear, multi-dimensional, and realistic form. This also facilitates remote consultations, maintenance support, and troubleshooting. It allows inspections and controls to be performed in hazardous or clean environments without the need for physical human presence.

Our website is under development.
For further information please contact us!